6 Important Parameters Setting of VFD
Selection of V/f Type
Selection of V/f type includes the maximum frequency, basic frequency and torque type. Maximum frequency refers to the highest frequency that the VFD & motor system can operate. As the maximum frequency of variable frequency drive may be higher, when the allowable maximum frequency of motor is lower than the maximum frequency of the VFD, it should be set according to the requirements of the motor and its load. Basic frequency is the demarcation line of VFD control motor’s constant power and constant torque, it shall be set according to the rated voltage of the motor. Torque type refers to whether the load is a constant torque load or a variable torque load, the user choose its type according to the V/f type diagram and load characteristics in the instructions for the use of VFD. Based on the actual situation and actual requirements of the motor, the maximum frequency is set to 83.4 Hz, and the basic frequency is set to 50 Hz. Load type: constant torque load below 50Hz and constant power load at 50-83.4Hz.
How to Adjust Starting Torque
Purpose of adjusting the starting torque is to improve the low-speed performance of the VFD when starting, so that the output torque of motor can meet the starting requirements of production. Torque control is rather complex in variable frequency speed control system of induction motor. In a low frequency band, the effect of resistance and leakage reactance can not be ignored. If V/f is constant, the flux will decrease, output torque of motor will also decrease thereof. So proper compensation shall be made to voltage in the low frequency band, so as to improve the torque. However, the influence of leakage impedance is not only related to frequency, but also to the magnitude of motor current. It is very difficult to compensate accurately. In recent years, some self-compensating converters have been developed, but they require massive computation and complex software, hardware, so compensation is manually set by users for general VFD.
How to Set Acceleration and Deceleration Time
RCF of variable frequency drive in starting and braking process is set by user. If the moment of inertia J and load of the motor increase or decelerate at a predetermined frequency, the acceleration torque may not be sufficient, thus resulting in the motor stall. Namely the motor speed is not in harmony with the output frequency of VFD, thus causing overcurrent or overvoltage. Therefore, the acceleration and deceleration time shall be set reasonably according to the moment of inertia and load of the motor, so that the RCF of VFD can be coordinated with the speed change rate of the motor. The method to check whether this setting is reasonable is to select the acceleration and deceleration time according to experience. If overcurrent occurs during start-up, the acceleration time can be prolonged appropriately. In case the overcurrent occurs during braking process, the deceleration time shall be prolonged appropriately. In the other hand, the acceleration and deceleration time shall not be set too long, otherwise the production efficiency would be affected, particularly the frequent starting and braking.
Frequency Jump
When the V/f controlled VFD drives an induction motor, current and speed of the motor will oscillate in some frequency bands. Seriously, the system can’t operate, or overcurrent protection occurs in the acceleration process to prevent the motor from starting normally, it’s more serious in a light load or small amount of spin. Frequency jump function is provided in common VFDs, and user can set the jump points and width of jump points on V/f curve based on the frequency oscillation point in the system. When the motor accelerates, it jumps these frequency bands automatically to ensure the normal operation of the system.
Overload Rate Setting
This setting is used for overload protection of the VFD and motor. When the output current of VFD is larger than the OL setting value determined by the overload rate setting value and the motor’s rated current, the variable frequency drive carries out overload protection (OL) with the inverse time characteristic, and stops output at the overload protection.
Setting of Motor Parameters
Setting parameters of VFD include the motor’s basic parameters, such as the motor power, rated voltage, rated current, rated speed, pole number. The setting of these parameters is very important as they will directly affect the normal performance of some protection functions in the VFD. They must be set correctly according to the actual parameters of the motor, so as to ensure the normal operation of variable frequency drive.
Selection of V/f type includes the maximum frequency, basic frequency and torque type. Maximum frequency refers to the highest frequency that the VFD & motor system can operate. As the maximum frequency of variable frequency drive may be higher, when the allowable maximum frequency of motor is lower than the maximum frequency of the VFD, it should be set according to the requirements of the motor and its load. Basic frequency is the demarcation line of VFD control motor’s constant power and constant torque, it shall be set according to the rated voltage of the motor. Torque type refers to whether the load is a constant torque load or a variable torque load, the user choose its type according to the V/f type diagram and load characteristics in the instructions for the use of VFD. Based on the actual situation and actual requirements of the motor, the maximum frequency is set to 83.4 Hz, and the basic frequency is set to 50 Hz. Load type: constant torque load below 50Hz and constant power load at 50-83.4Hz.
How to Adjust Starting Torque
Purpose of adjusting the starting torque is to improve the low-speed performance of the VFD when starting, so that the output torque of motor can meet the starting requirements of production. Torque control is rather complex in variable frequency speed control system of induction motor. In a low frequency band, the effect of resistance and leakage reactance can not be ignored. If V/f is constant, the flux will decrease, output torque of motor will also decrease thereof. So proper compensation shall be made to voltage in the low frequency band, so as to improve the torque. However, the influence of leakage impedance is not only related to frequency, but also to the magnitude of motor current. It is very difficult to compensate accurately. In recent years, some self-compensating converters have been developed, but they require massive computation and complex software, hardware, so compensation is manually set by users for general VFD.
How to Set Acceleration and Deceleration Time
RCF of variable frequency drive in starting and braking process is set by user. If the moment of inertia J and load of the motor increase or decelerate at a predetermined frequency, the acceleration torque may not be sufficient, thus resulting in the motor stall. Namely the motor speed is not in harmony with the output frequency of VFD, thus causing overcurrent or overvoltage. Therefore, the acceleration and deceleration time shall be set reasonably according to the moment of inertia and load of the motor, so that the RCF of VFD can be coordinated with the speed change rate of the motor. The method to check whether this setting is reasonable is to select the acceleration and deceleration time according to experience. If overcurrent occurs during start-up, the acceleration time can be prolonged appropriately. In case the overcurrent occurs during braking process, the deceleration time shall be prolonged appropriately. In the other hand, the acceleration and deceleration time shall not be set too long, otherwise the production efficiency would be affected, particularly the frequent starting and braking.
Frequency Jump
When the V/f controlled VFD drives an induction motor, current and speed of the motor will oscillate in some frequency bands. Seriously, the system can’t operate, or overcurrent protection occurs in the acceleration process to prevent the motor from starting normally, it’s more serious in a light load or small amount of spin. Frequency jump function is provided in common VFDs, and user can set the jump points and width of jump points on V/f curve based on the frequency oscillation point in the system. When the motor accelerates, it jumps these frequency bands automatically to ensure the normal operation of the system.
Overload Rate Setting
This setting is used for overload protection of the VFD and motor. When the output current of VFD is larger than the OL setting value determined by the overload rate setting value and the motor’s rated current, the variable frequency drive carries out overload protection (OL) with the inverse time characteristic, and stops output at the overload protection.
Setting of Motor Parameters
Setting parameters of VFD include the motor’s basic parameters, such as the motor power, rated voltage, rated current, rated speed, pole number. The setting of these parameters is very important as they will directly affect the normal performance of some protection functions in the VFD. They must be set correctly according to the actual parameters of the motor, so as to ensure the normal operation of variable frequency drive.
Post a Comment:
You may also like:
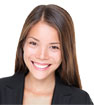
Variable Frequency Drives

Featured Articles
How Does Variable Frequency Drive ...
The rotating speed of inductor type AC motor (hereinafter referred to as motor) is determined by the number of pole and ...
Can I Run a 60Hz Motor on 50Hz by ...
We are often asked “can the motor with a rated frequency of 60Hz operate at 50Hz (vice versa)?” When the motor is operated at a ...
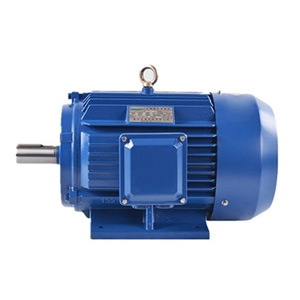