Home » Application » Benefits of Variable Frequency Drive in Injection Molding Machine
Benefits of Variable Frequency Drive in Injection Molding Machine
Injection molding machine is the main molding processing equipment for various injection molding materials (such as polyethylene, polypropylene). The whole working process of molding processing equipment can be divided into several stages, including mold closing, mode locking, glue injection, glue melting, pressure maintaining, cooling and mold opening, each stage requires different working pressure and flow. Taking the oil pump motor as an example, the whole injection process is in a changing load state.
At present, most injection molding machines adopt the constant rate pump, correspondingly, the oil pump motor transfers constant rotational speed to constant output flow. During the processing, some stages require only a few flow and pressure, remaining hydraulic oil flows back to oil tank through the overflow valve. According to previous theoretical experience, the processed parts don’t work under the maximum pressure or flow, so a huge margin is generated, and a certain amount of loss produces.
On the problem of energy consumption for high pressure throttle, some injection molding machine manufacturers have developed variable pump injection molding machine. Assuming that the constant rate pump is changed to the variable pump, both the working contents and costs are huge, so it’s unreasonable to change the existing constant rate pump to variable pump. Now, more and more injection molding machines adopt the variable frequency drive, which not only solves the defects of injection molding machine, but also brings other advantages. Such as:
1.Soft start: Under the power frequency, the motor adopts a star triangle step-down delay starting, and the starting current is 4~7 times of the motor’s rated current. If several high-power motors start at a same time, they will impose a great impact on the power grid. However, the variable frequency motor can start softly at the rated current, the current is smooth without impact, thus reducing the impact on the motor and the power grid, extending the motor’s service life.
2. Avoid personal safety accidents: after installing the VFD, velocity analogue of the machine’s computer would be unable to output when the operator pick up, clean and maintain modules on the injection molding machine, the motor would be in suspension state and hydraulic system has no pressure, thus avoiding malfunction of the injection molding machine, and preventing the occurrence of personal safety accidents.
3. Reduce reactive power: Reactive power not only increases line loss and equipment heating. More importantly, it results in the reduction of active power caused by the reduction of power factor. After applying the variable frequency drive, the power factor is close to 1 due to the filter capacitor in the VFD, active power of the power grid is greatly increased, thus saving the energy consumption caused by reactive power.
4. Energy conservation: Three sets of asynchronous AC motors commonly used in the injection molding machine can’t change the speed, so the flow of constant flow paddle pump and hydraulic fluid it drives can’t be changed. When the injection molding machine operates at a medium and low speed, redundant flow flows back to the oil tank through the overflow valve, thus causing a great energy loss. VFD can adjust the motor speed according to the command of control system, so as to make sure that flow of hydraulic oil output by paddle pump can be varied according to the operation requirements of the injection molding machine, thus reducing the energy loss caused by back flow of hydraulic oil from the overflow valve to the oil tank, saving a massive amount of power energy. Electricity saving rate of motor power consumption is about 20-70%. It’s a necessary trend for the injection molding machine to add VFD.
At present, most injection molding machines adopt the constant rate pump, correspondingly, the oil pump motor transfers constant rotational speed to constant output flow. During the processing, some stages require only a few flow and pressure, remaining hydraulic oil flows back to oil tank through the overflow valve. According to previous theoretical experience, the processed parts don’t work under the maximum pressure or flow, so a huge margin is generated, and a certain amount of loss produces.
On the problem of energy consumption for high pressure throttle, some injection molding machine manufacturers have developed variable pump injection molding machine. Assuming that the constant rate pump is changed to the variable pump, both the working contents and costs are huge, so it’s unreasonable to change the existing constant rate pump to variable pump. Now, more and more injection molding machines adopt the variable frequency drive, which not only solves the defects of injection molding machine, but also brings other advantages. Such as:
1.Soft start: Under the power frequency, the motor adopts a star triangle step-down delay starting, and the starting current is 4~7 times of the motor’s rated current. If several high-power motors start at a same time, they will impose a great impact on the power grid. However, the variable frequency motor can start softly at the rated current, the current is smooth without impact, thus reducing the impact on the motor and the power grid, extending the motor’s service life.
2. Avoid personal safety accidents: after installing the VFD, velocity analogue of the machine’s computer would be unable to output when the operator pick up, clean and maintain modules on the injection molding machine, the motor would be in suspension state and hydraulic system has no pressure, thus avoiding malfunction of the injection molding machine, and preventing the occurrence of personal safety accidents.
3. Reduce reactive power: Reactive power not only increases line loss and equipment heating. More importantly, it results in the reduction of active power caused by the reduction of power factor. After applying the variable frequency drive, the power factor is close to 1 due to the filter capacitor in the VFD, active power of the power grid is greatly increased, thus saving the energy consumption caused by reactive power.
4. Energy conservation: Three sets of asynchronous AC motors commonly used in the injection molding machine can’t change the speed, so the flow of constant flow paddle pump and hydraulic fluid it drives can’t be changed. When the injection molding machine operates at a medium and low speed, redundant flow flows back to the oil tank through the overflow valve, thus causing a great energy loss. VFD can adjust the motor speed according to the command of control system, so as to make sure that flow of hydraulic oil output by paddle pump can be varied according to the operation requirements of the injection molding machine, thus reducing the energy loss caused by back flow of hydraulic oil from the overflow valve to the oil tank, saving a massive amount of power energy. Electricity saving rate of motor power consumption is about 20-70%. It’s a necessary trend for the injection molding machine to add VFD.
Post a Comment:
You may also like:
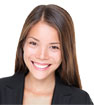
Variable Frequency Drives

Featured Articles
Variable Frequency Drive for Food ...
Nowadays the food machinery industry has been rapidly developed. As the motor drive, variable frequency drive will change the ...
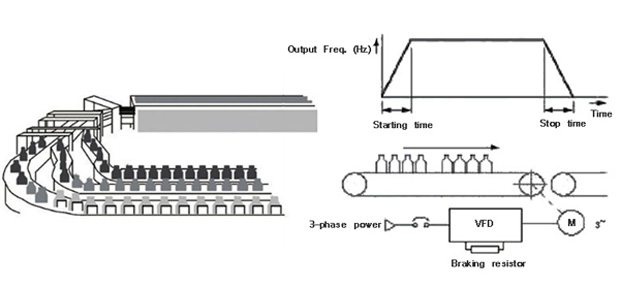
Variable Frequency Drive for Fans
Fan is a kind of machine that compresses and conveys gas. If the pressure of exhausted air is quite low, the fan plays a role of ...
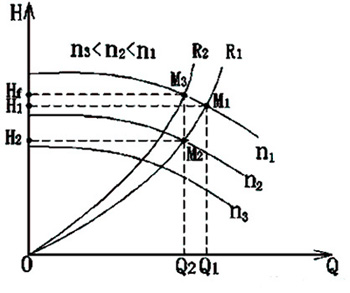