VFD Braking Unit and Braking Resistor
In the variable frequency drive speed control system, speed reduction and shutdown of the motor are realized by gradually reducing the frequency. When the frequency decreases, synchronous speed of the motor decreases accordingly, however, because of mechanical inertia, the rotational speed of motor rotor remains unchanged. When the synchronous speed is less than the rotor speed, the phase of rotor current changes almost 180 degrees, and the motor changes from the electrified state to the power generation state. Meanwhile, torque on the motor shaft becomes the braking torque, which makes the motor speed to decrease rapidly, and the motor turns to the regenerative braking state.
Regenerated power of the motor is fed back to the DC circuit after full-wave rectification by a fly-wheel diode. As the power of DC circuit can’t be fed back to the power grid through the rectifier bridge, it’s only absorbed by the capacitance of VFD. Although other parts can consume energy, the capacitance still has a short time of charge accumulation, thus forming a “pump-up voltage” to make the DC voltage rise. Excessive DC voltage will damage some parts of the variable frequency drive. Therefore, necessary measures must be taken to deal with this part of regenerative energy when the load is in power generation braking state. Methods to deal with the regenerative energy include dynamic braking method and feedback braking.
In the dynamic braking method, a discharging resistance unit is added to the DC side of the VFD to consume the regenerative energy on the power resistance, thus realizing the braking. This is the most direct way to deal with regenerated energy. It consumes regenerated energy on the resistance through a special energy consumption braking circuit and converts the energy into heat energy, so it is also called “resistor braking”. It includes the braking unit and braking resistor.
Braking Unit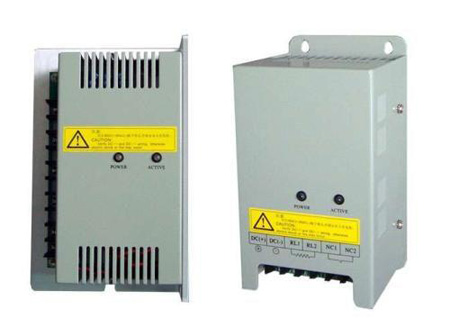
The function of braking unit is to connect the energy consumption circuit and ensure the DC circuit to release energy by thermal energy after passing through the braking resistor when the voltage Ud of the DC circuit exceeds the prescribed limit, such as 660V or 710V. The braking unit can be divided into two types: built-in type and external type. The former is suitable for low-power general-purpose VFD, while the latter is suitable for high-power VFD or conditions with special braking requirements. GK3000 series VFDs under 22KW have built-in braking units.
In principle, there’s no difference between the two, they are all “switches” to connect the braking resistor, and they consists of power transistor, voltage sampling and comparison circuit and driving circuit.
Braking Resistor
Braking resistor is the carrier used to consume the regenerative energy of the motor in the form of heat energy, it includes two important parameters of resistance value and power capacity. Generally, the ripple resistance and aluminum alloy resistance are mostly selected in engineering: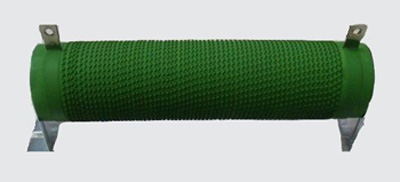
Regenerated power of the motor is fed back to the DC circuit after full-wave rectification by a fly-wheel diode. As the power of DC circuit can’t be fed back to the power grid through the rectifier bridge, it’s only absorbed by the capacitance of VFD. Although other parts can consume energy, the capacitance still has a short time of charge accumulation, thus forming a “pump-up voltage” to make the DC voltage rise. Excessive DC voltage will damage some parts of the variable frequency drive. Therefore, necessary measures must be taken to deal with this part of regenerative energy when the load is in power generation braking state. Methods to deal with the regenerative energy include dynamic braking method and feedback braking.
In the dynamic braking method, a discharging resistance unit is added to the DC side of the VFD to consume the regenerative energy on the power resistance, thus realizing the braking. This is the most direct way to deal with regenerated energy. It consumes regenerated energy on the resistance through a special energy consumption braking circuit and converts the energy into heat energy, so it is also called “resistor braking”. It includes the braking unit and braking resistor.
Braking Unit
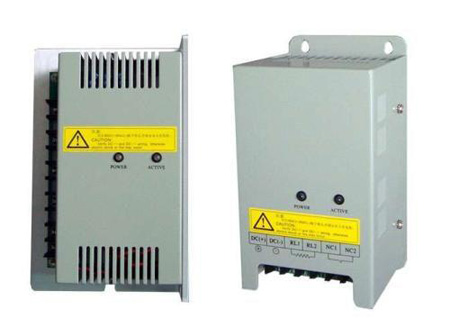
The function of braking unit is to connect the energy consumption circuit and ensure the DC circuit to release energy by thermal energy after passing through the braking resistor when the voltage Ud of the DC circuit exceeds the prescribed limit, such as 660V or 710V. The braking unit can be divided into two types: built-in type and external type. The former is suitable for low-power general-purpose VFD, while the latter is suitable for high-power VFD or conditions with special braking requirements. GK3000 series VFDs under 22KW have built-in braking units.
In principle, there’s no difference between the two, they are all “switches” to connect the braking resistor, and they consists of power transistor, voltage sampling and comparison circuit and driving circuit.
Braking Resistor
Braking resistor is the carrier used to consume the regenerative energy of the motor in the form of heat energy, it includes two important parameters of resistance value and power capacity. Generally, the ripple resistance and aluminum alloy resistance are mostly selected in engineering:
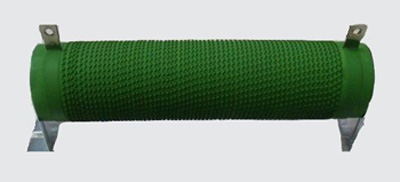
- The ripple resistance adopts vertical surface ripple to facilitate heat dissipation and reduce parasitic inductance, uses high flame retardant inorganic coating to effectively protect resistance wire from aging, thus extending its service life.
-
The aluminum alloy resistance has weather resistance and vibration resistance, is superior than traditional ceramic skeleton resistors and widely used in harsh industrial control environment with high requirements. It can be installed in compact spaces or added with radiators.
Post a Comment:
You may also like:
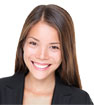
Variable Frequency Drives

Featured Articles
What is a Variable Frequency Drive
Variable frequency drive (VFD) is an adjustable speed drive used for motor drive system, control the speed and torque of the AC ...
